Altrad contributes shoring solution for large-scale excavation in Abu Dhabi
24 October 2024
UK-based provider of formwork, falsework/shoring, heavy-duty support, ground shoring and safety and access systems Altrad RMD Kwikform (Altrad) said it supplied shoring solutions on “one of the largest excavations in the company’s history” in Abu Dhabi, United Arab Emirates (UAE).
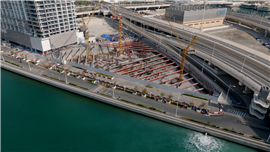
The scheme is for a new city centre mixed-used development in the UAE’s capitol city, which will integrate commercial and residential spaces. At the core of the project is a large basement excavation (measuring about 14m deep and 70m wide with an approximate volume of 111,000m3) in a dense urban setting surrounded by waterfront.
Altrad said it “was tasked with delivering a system that could handle the extensive loads and provide robust support throughout the excavation process.
“This role was crucial in ensuring that the shoring solution not only met the technical requirements, but also adhered to the project’s timeline and budgetary constraints.”
Unique shoring solutions for Abu Dhabi’s city centre
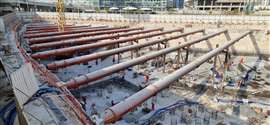
In addition to the crowded urban setting, the site also had abutting waterfronts on two sides of the work area, which also posed challenges.
“The proximity to the water required careful planning to prevent contamination as well as mitigating risks associated with flooding and erosion,” said Altrad.
Altrad used 387 tonnes of its Tubeshor material (consisting of 24 Tubeshor props each with a 1,06cm diameter). The props had a maximum span of 67m and prop spacing of 7.5m, which was supported by a single plunge column along the length.
“The Tubeshor system’s strength and modular design made it the ideal solution for the project’s complex requirements,” said Altrad, adding the solution also “enabled a value-engineered strutting design, which brought significant benefits to the project.
“By utilising high-strength S460 steel,” Altrad continued, “the Tubeshor system provided exceptional structural support giving unprecedented axial load capacity, with the maximum load acting on the prop of 3,295kN [kilonewton].”
Altrad said the strategy led to a 30% reduction in the amount of steel needed, which lowered costs and maximised the available (and limited) excavation space. Bolted connections also improved the ease of use and reduced installation and dismantling time, the firm said.
Equipment was on site for more than 12 months.
“Weldable stub ends were used on one end of the prop to reduce welding and installation time on site, while allowing for a certain amount of length adjustment,” Altrad said.
Reducing material needs with flexible shoring strategies
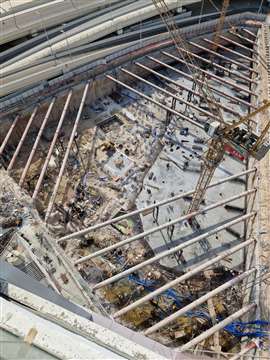
Flexibility and manoeuvrability were also touted, with Altrad saying it was able to deliver fewer plunge columns than originally designed, leading to a more streamlined process.
“The ability to easily adjust and reconfigure the props on-site meant that the system could be tailored to meet the specific needs of the excavation as it progressed,” Altrad said. “The original customer design had featured 28 plunge columns, but the team were able to reduce this to 10.”
Vijay Patil, lead engineer for Altrad RMD Kwikform in the Middle East and India, confirmed this was one of the company’s largest excavation projects to date.
“The sheer scale of the project showcases Tubeshor’s engineering and adaptability in providing robust and efficient support for complex construction projects, and this is one of the largest excavations in Altrad RMD Kwikform’s history,” he said.
STAY CONNECTED

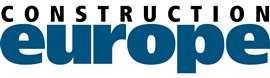
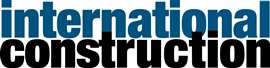
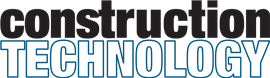
Receive the information you need when you need it through our world-leading magazines, newsletters and daily briefings.
CONNECT WITH THE TEAM
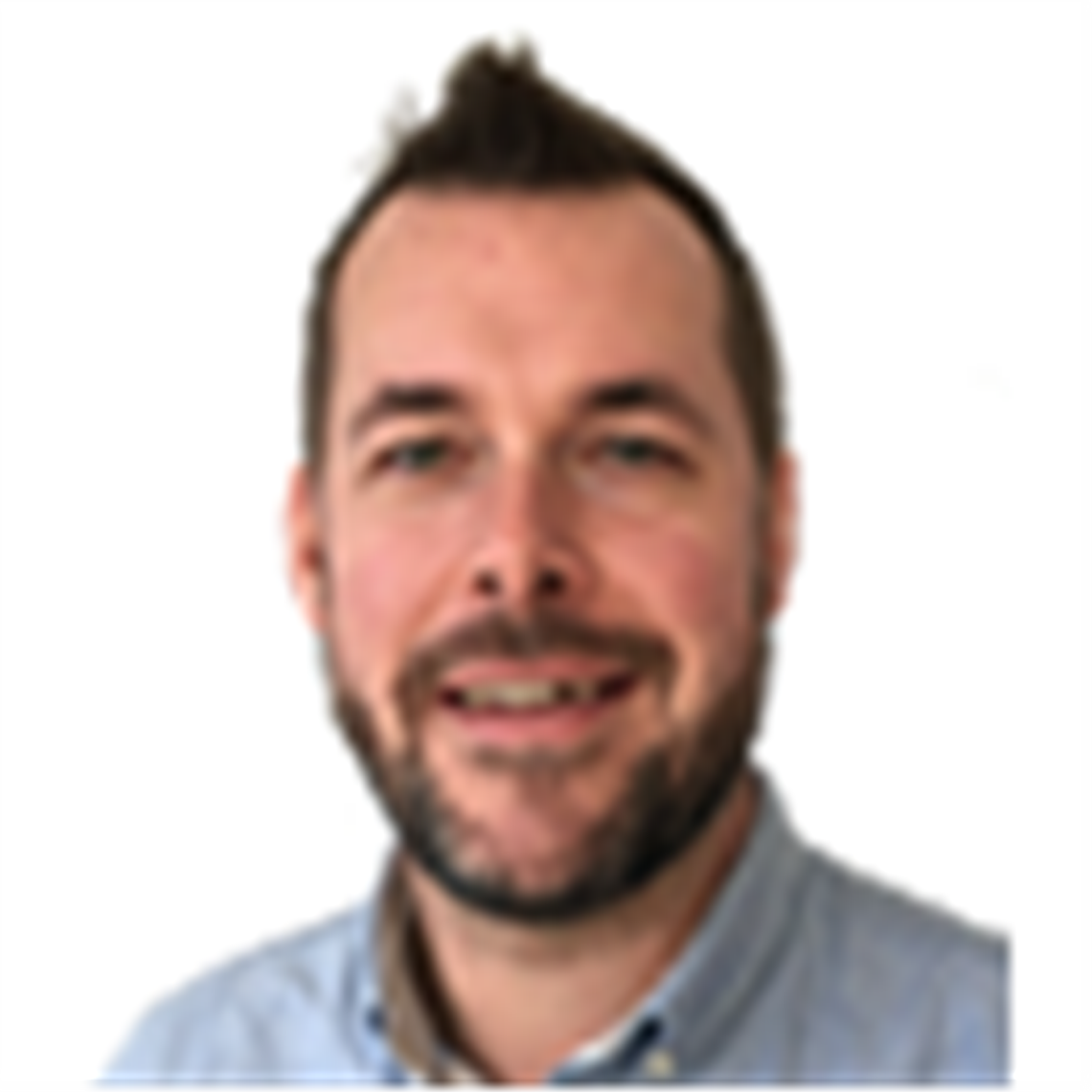
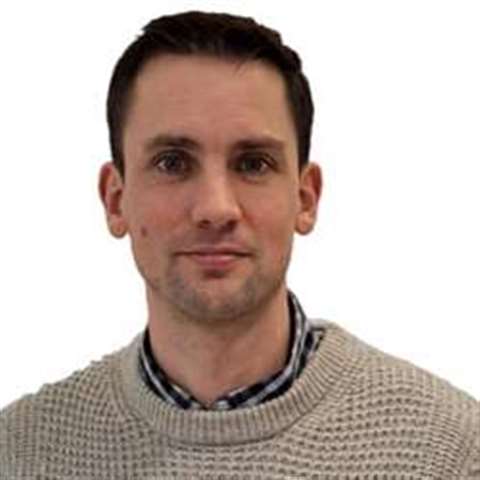
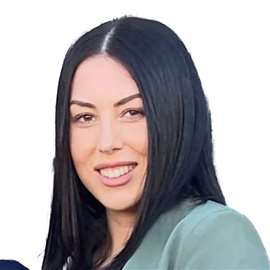
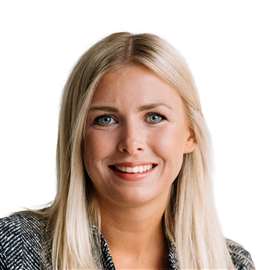